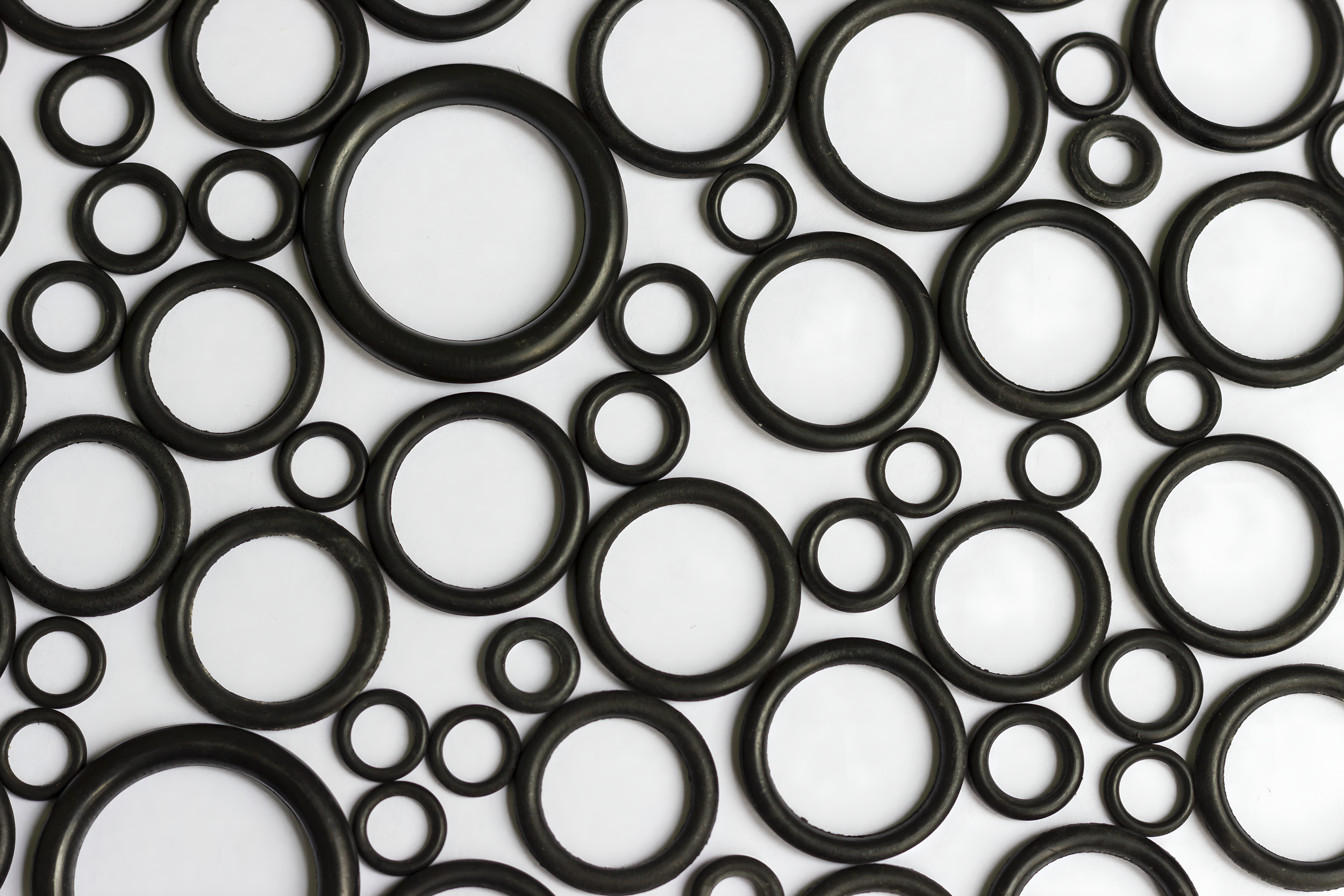
Elongation
Elongation is defined as the length at the point of rupture expressed as a percentage of the original length (i.e., the length at rest). If rubber reaches twice its original length before breaking, its elongation is 100%.
Importance:
For an elastomer to meet the mechanical requirements for its intended use, it is essential to measure the force required to bring a sample to its point of rupture. Understanding the elongation of elastomers is crucial for determining the best suitability for customers. Stretching a sample of rubber will cause deformation in its shape. The more the sample elongates, the more parts of it will shrink until it ultimately breaks.
Measurement:
The testing method determines the variability between vulcanized rubber samples and the influence of parameters affecting load-stress characteristics, such as temperature, relative humidity, and pre-treatment of the rubber.
The testing device, called a dynometer, includes an extensometer that optically or mechanically tracks two markings on the sample. The dynometer can continuously measure the size of the rubber test sample during the elongation phase and at the point of rupture.
Samples shaped like a dog bone are stretched in the narrow area where the two markings are placed. O-ring samples are sometimes twisted during the stretching to prevent any specific area from being affected. The speed of rotation is included in the results.
Calculation:
When using markings or an extensometer to define a specific test segment, only this length is used for the calculation; otherwise, the distance between the grip points is used as the original measured length.
Results/Reporting:
Elongation is expressed as a percentage and reported to two decimal places.
Percentage Elongation = (Elongation at Break) × 100 / (Original Measured Length)